It sounds somewhat futuristic, but today building with CO² is possible. Thanks to accelerates carbonation, CO² is used to produce building material. A sustainable footpath in Ghent illustrates how promising this new technology is.
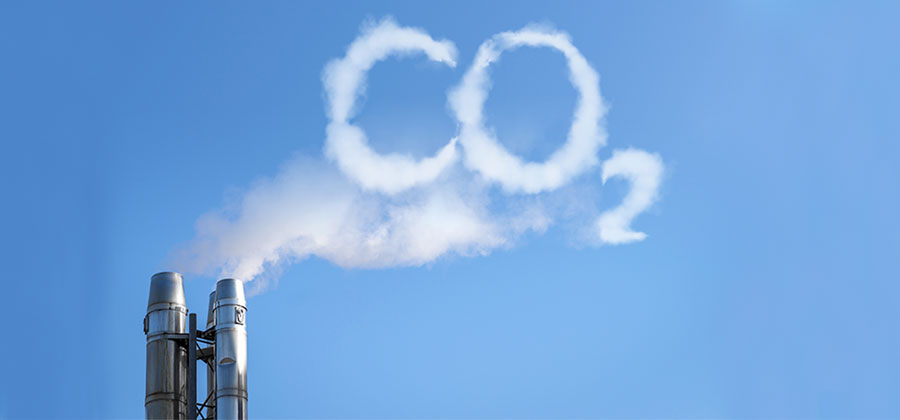
In mid-December, CO2 Value Europe, a think- and do- tank representing the carbon capture and utilisation (CCU) community in Europe, held a webinar about the use of CO2 to create building material. Concrete examples of this sustainable technology were given to illustrate the potential they can offers, especially in the hard-to-abate construction sector. BNP Paribas Fortis and CO2 Value Europe are partners in issues related to financing innovative and sustainable technologies. As an institution, we work hard to promote corporate sustainability.
The second-most polluting industrial sector
As well as being one of the largest in the world, the cement industry's high levels of flue gas emissions also make it one of the most polluting. Cement is a crucial component in concrete, which is vital for the building sector. A sustainable alternative to cement could make a huge difference. One option here is carbonation, also known as CO2 mineralization. While this CCU technology is not yet well known, it has the potential to play a crucial role in mitigating climate change.
Giving nature a helping hand
Carbonation is a natural process, where minerals react with CO2 to create e.g. limestone and dolomite. In nature, this process takes thousands of years, but today, thanks to innovative methods, this time can be cut down to some minutes. This process requires relatively small amounts of energy and can be used to create several different products, including bricks where CO2 is sequestered permanently.
CO2 all the way
The development of CCU technology has accelerated sharply in recent years. We now have cement alternatives that meet the building sector’s technical requirements. There are various ways to store CO2 into construction materials. For example, CO2 can be injected as an alternative to water for hardening cement. What’s more, CO2 can be used to convert mineral waste from steel and mining industries into new products such as aggregates, which can be used as a basis for paving or building blocks.
Good for the planet
Mineralization of CO2 has a significant impact on the environment, because it has an effect at different levels. The annual global reduction in CO2 emissions is estimated to be 250 - 500 million tonnes by 2030 (source CO2 Value Europe).
- CO2 can be captured from flue gas emitted by industrial processes used to create steel, cement, and chemicals, with no need for concentration or treatment.
- CO2 can be captured directly from the atmosphere to create negative carbon emissions, i.e. carbon removal.
- In both cases, the CO2 will be stored permanently in building materials.
- Mineral waste and even construction waste are used together with CO2 to make new building materials, so it reduces landfills and the associated costs.
- Recycling carbon and construction wastes means fewer new natural resources are exploited.
What’s the catch?
New developments are never without their challenges, and this is no exception. Offering a competitive, quality alternative to concrete in a circular economy requires investment and adaptation.
- Factories will have to adapt their plants. Locating them close to significant sources of CO2, like a steel factory, is recommended so the CO2 and the waste fractions do not have to be transported.
- Manufacturing new products takes energy and creates CO2 emissions, even if the products are made using carbon dioxide and waste. It is why renewable energy should be used as much as possible to increase the sustainability of the processes.
- The commercialization of accelerated carbonation technologies is quite recent, and some processes are not optimally equipped for this yet.
- The lack of appropriate regulatory frameworks is also a drawdown to allow for a fast deployment of CCU technologies. This is an area CO2 Value Europe is especially working on.
Despite these challenges, Andre Bardow (Professor of Energy & Process Systems Engineering, ETH Zurich) told us during the webinar that he is convinced CO2 mineralization reduces the CO2 footprint from a life cycle perspective, even more than carbon capture and storage (CCS).
Zero domestic waste
There are already companies producing low-CO2 construction materials around the world. One of them is in Limburg. Orbix, in Genk, has successfully extracted minerals from steel production waste (known as slag) which are used as a basis for eco-friendly concrete stone. Not only is liquid CO2 used to produce concrete stone rather than polluting cement, but residual waste that would otherwise be dumped in landfill is also recycled.
There is a great example of this in Ghent, where Orbix worked with the Flemish research institute VITO to create the Stapsteen project for the city. Visitors can walk on Belgium’s first-ever circular economy footpath in the Leewstraat: 100m2 made entirely from sustainable bricks, saving a full 2 tonnes of CO2.
Do you have sustainability plans for 2021? Our experts at the Sustainable Business Competence Centre can provide advice about innovations like CO2 mineralisation and support your sustainable transition.
18.11.2020
Joining forces for a low-carbon economy – our bank's contribution to CO2 Value Day Europe
The fourth CO2 Value Day took place online on 10 November. The event, which we helped set up as one of its partners, focused on the progress made in developing the CCU industry.
At BNP Paribas Fortis, we were delighted to help stage this event. The subject of carbon capture and utilisation (CCU) lies close to our heart as we strive toward a low-carbon economy.
About CCU and CO2 Value Europe
Carbon capture and utilisation encompasses all industrial processes aimed at capturing carbon dioxide – from industrial sources or directly from the air – and converting it into usable products. Today, carbon is not simply a waste material; it can be reused as a raw material for a host of applications, including building materials, fuel production and in the chemical industry.
CO2 Value Europe, a European organisation founded in 2017, aims to promote the development and market introduction of these sustainable industrial solutions and thus contribute to reducing global CO2 emissions and diversifying the raw material base away from fossil fuels and gas. The organisation brings together more than 50 companies from various sectors across Europe, including 12 multinationals. As its only financial partner, we support CO2 Value Europe by giving the organisation access to our expertise and network.
The event
The CO2 Value Day is a unique opportunity for all members of CO2 Value Europe to assess the overall progress made in developing the CCU industry. This year, the event was once again a mix of plenary presentations, keynote speeches and interactive workshops.
After a welcome and introduction by Stefanie Kesting, Chair of CO2 Value Europe, Sebastien Soleille took to the floor. As Global Head of Energy Transition & Environment at our bank, he discussed the role banks play in supporting sustainable development. This is a responsibility that we do not take lightly at BNP Paribas Fortis, and we've been helping companies with their sustainable transition for years through our Sustainable Business Competence Centre. We focus on four pillars: decarbonisation, the circular economy, human capital and smart cities.
Vincent Basuyau, Policy Officer at DG GROW, then shed some light on CCU when it comes to current EU policy. This primarily concerned the Innovation Fund, established by the European Union to invest in innovative projects that decarbonise industrial activities in Europe.
The plans for 2021 were also unveiled. In the coming year, CO2 Value Europe will focus above all on the ongoing development of and market uses for CCU technologies. The aim is to coordinate the many different players involved in CO2 use in Europe, integrate their efforts into the value chain and become the ambassador of the CO2 user community towards policy-makers and financiers. After all, a favourable legal and market framework is a prerequisite for the commercial roll-out of CCU solutions.
CO2 Value Europe aims to encourage the ongoing development of CCU technologies by:
- offering solutions to decrease net CO2 emissions from hard to abate sectors, such as energy-intensive process industries (e.g. cement and lime mortar, chemicals, steel and other metals) and the transport sector;
- creating negative emissions in sequestering CO2 in building materials resulting from the carbonation of mineral waste;
- providing an alternative raw material for the production of chemical building blocks and to replace fossil fuels and gas;
- facilitating the storage and transport of renewable energy, speeding up the transition of energy systems in the EU;
There was also time for two break-out sessions, with the first focusing on developing a strategy to create a regulatory framework that supports the deployment of CCU technologies.
The second session concerned projects and financing. Aymeric Olibet, Sustainable Business Advisor at BNP Paribas Fortis, talked about a range of topics, including the solutions we offer companies through our Sustainable Business Competence Centre, financing sustainable projects through green bonds and green loans, and blended finance (a mix of public and private funding).
Finally, attendees had the chance to meet other participants during online speed meetings.
29.10.2020
First green hedge in Belgium becomes a reality
BNP Paribas Fortis has become the first bank in Belgium to launch a green hedge. With this product, the bank gives clients the opportunity to integrate their sustainable objectives deep into their business operations.
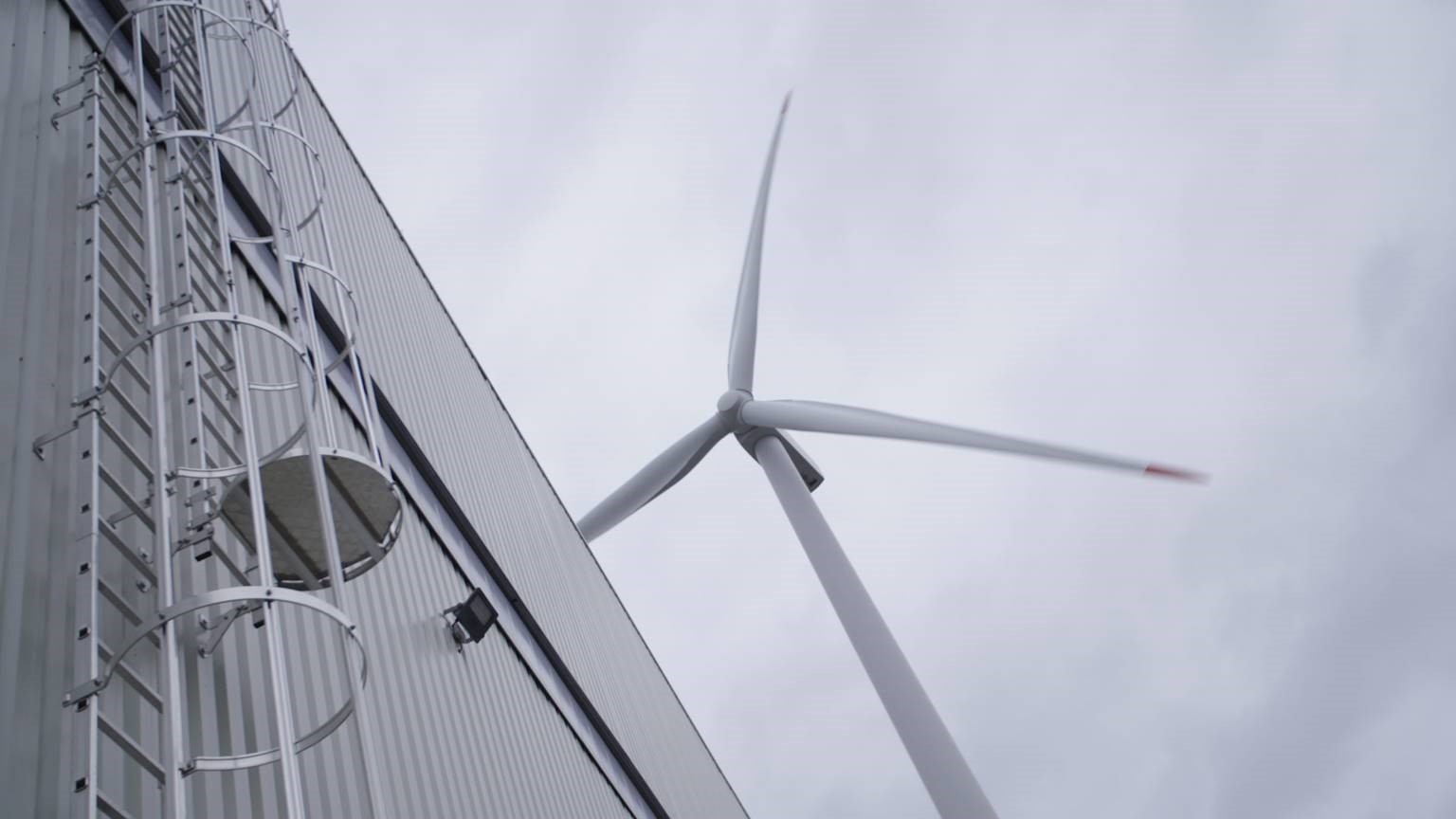
Sustainability is now embedded in almost every company's mission. Companies undertake numerous ecological initiatives and finance sustainable investments with green loans. BNP Paribas Fortis is going one step further and is also offering its clients the opportunity to cover the financing risk with a sustainable hedge.
A Belgian first
The first green interest rate hedge in Belgium has become a reality. "We are delighted and proud to be able to achieve this first with Katoen Natie as true partners", explains Filip Moens, Head of Corporate Solutions in the trading room at BNP Paribas Fortis. "Katoen Natie already had a green loan with us and wanted to hedge the interest rate risk by switching from a variable to a fixed interest rate using an interest rate swap. Instead of opting for an ordinary interest rate hedge, we have attached additional green terms and conditions that mean Katoen Natie is strengthening its sustainable commitment."
Katoen Natie carried out an interest rate swap, but a green hedge can also be applied to exchange rate or inflation risks. Moreover, having an existing green loan is not a requirement.
Sustainable safety net
The green hedge stimulates sustainability, but goes even further and provides a green safety net, with the client paying a sustainability premium if the proposed terms and conditions are not met. BNP Paribas Fortis does not receive this premium itself, but instead invests it in an environmental project chosen in advance. "At Katoen Natie, for example, we chose a project that plants trees. The effect of this product is therefore twofold. On the one hand, it is an incentive for the client to actually fulfil their ecological commitment. However, if they fail to do so for any reason, the additional premium they pay will be spent on a green project. So it's a win-win situation for the environment", says Filip Moens.
Tailored to your business
"The strength of this product lies in its broad application", emphasises Filip Moens.
"Companies who do not have a green loan but want to integrate more sustainability into their corporate culture, can really make this ambition a reality thanks to the green hedge. The green terms and conditions linked to it are determined by mutual consultation. A lot is possible as long as these are sufficiently ambitious, achievable and measurable. These include switching to 80% renewable energy, making the fleet 100% electric in five years' time, and collecting litter as an annual team-building exercise. Companies can define conditions that are perfectly in line with their corporate culture. The same applies to the back-up project that we finance if the conditions are not met. Here, too, they can opt for a local project close to their heart."
No empty promises
A green hedge reinforces existing green projects and firmly underlines an active green commitment. This therefore concerns more than image. "This product integrates sustainability deeply into business operations and requires a serious and firm commitment from clients", says Filip Moens. "They have to be really motivated to do something about the environment. There is quite a lot of administration involved, such as an annual evaluation report and external audits. However, clients really do make a difference with this green choice."
As a true partner, BNP Paribas Fortis wants to make a positive contribution to companies' projects and growth. The green hedge is in line with companies' current sustainable mindset and fits perfectly with the bank's strategy: to build a positive, sustainable and clean future together with clients.
25.07.2018
Creative uses for construction waste
Most construction waste is recycled in one way or another. However, sometimes direct reuse is possible and valuable heritage can be given a second life.
Construction and demolition waste accounts for 20% of our total waste. Over 90% is reused. Sometimes via high-quality recycling, and sometimes via 'downcycling'. In the latter case, the rubble is ground up and used as granular material for road foundations. Some companies have found unique ways of taking demolition waste and fully or partially reusing it, rather than recycling it.
Schoenen Torfs are proud of 'Ten Afval'. It's a recycling project that first and foremost benefits their employees. When the company renovates one of its seventy shops, the employees are free to dismantle and empty the interior themselves. Furniture, flooring, lighting, decorations: employees can take all of it home with them.
"As a result of 'Ten Afval', the materials that are removed from the waste stream are given a second life," explains manager Wouter Torfs in Trends magazine. "It's a real win-win situation: it's better for the environment, we don't need to hire a contractor or pay landfill costs, and it keeps our employees happy."
The golden ceiling
Rotor Deconstruction has made reusing old construction materials in new projects its core business. For each demolition, this waste processing company assesses which materials are valuable enough to finance the dismantling. An excellent example of this process is the dismantling of the BNP Paribas Fortis building in Ravenstein. The building dated from 1971. The counters, strongroom, lifts and executive offices of the former Generale Bank were designed by the famous Belgian interior architect and furniture designer, Jules Wabbes.
The old 'golden ceiling' that Wabbes designed - false ceilings made from aluminium coated in gold-coloured lacquer - was repurposed in many different ways. Plusofficearchitects reused parts of the ceiling in the new auditorium of the municipal library in Sint-Pieters-Woluwe. Another piece of the golden ceiling is now hanging in Emilie Pharmacy in Schaarbeek, which architect Nathalie De Leeuw renovated for pharmacist Saïd Bounouch. The architect suggested using as many reclaimed materials as possible and went with Bounouch to browse the Rotor showroom. The gold-lacquered aluminium grille is now the focal point of the pharmacy. In the entrance, a piece of the bank's old granite floor and a few panels with photo prints by interior architect and designer Christophe Gevers were reclaimed. This gave these culturally valuable pieces of Brussels' history a new place and function in the city. Rotor Deconstruction was awarded the OVAM Ecodesign Award PRO for this project.
20.12.2024
Mobility in 2025: Arval’s view
Laurent Mélignon, Corporate Sales Director of Arval, the market leader in full-service car leasing and new mobility solutions, looks ahead to 2025. What does the future hold for the industry and mobility?
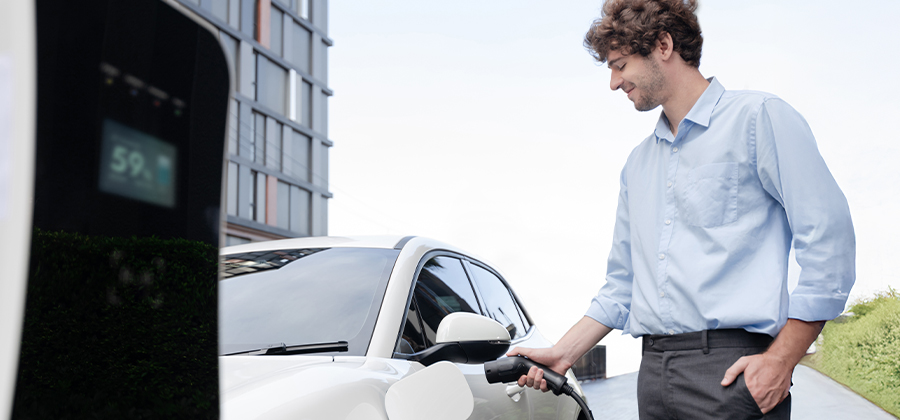
Arval is part of the Commercial, Personal Banking & Services division of the BNP Paribas Group. As the market leader, it plays a key role in offering full-service car leasing and new mobility solutions. Laurent Mélignon, Corporate Sales Director of Arval, is thus ideally placed to share his thoughts on what's in store for Arval in 2025.
Arval is the market leader in a sector in flux: how companies and private individuals see and approach mobility has changed significantly. Mélignon sees several reasons for this: "In our country, taxation is the primary driver of many change processes. This taxation is linked to wage costs: many companies see company cars as a tax-friendly alternative for maximising the remuneration they want to pay their staff. Employees, meanwhile, see company cars as a way to be compensated with tangible benefits, without the tax authorities targeting them. In the coming year, the tax framework will continue to evolve in line with this social evolution. The federal mobility budget and the bicycle allowance, for example, or options such as the cafeteria plan or the flex income plan: these are just some of the ways in which companies can use their salary package to motivate their workers."
But Arval's Corporate Sales Director sees even more drivers of change for mobility. Mélignon: "Our entire mobility culture is also changing, a trend that is set to continue in 2025. The younger generation is much less attached to the status that company cars have been associated with for so many years. They are just as happy to hop on a bicycle, take the bus or use car sharing, depending on the company's location, of course. Finally, there are also several macroeconomic factors driving this change. These include the growing traffic crisis many cities are facing, as well as the increasing awareness of people and economic players regarding the energy transition. We are all gradually seeing the need for change and alternative mobility choices. This has been clear for quite some time."
Flexible complexity
The mobility mix will only become stronger in the future. Mélignon: "That is a big part of our mission: to be and remain a one-stop shop, offering companies the opportunity to think in terms of flexible remuneration. A new employee, for example, someone who is single and without a family, has different mobility needs than their colleague, who is married with two children and has their own home in the countryside or in the city. Now that this need is becoming stronger and more established, Arval is the ideal partner to provide companies with knowledge about mobility and take the burden off their hands. We enable employers to offer flexibility by taking care of the complexity associated with it."
Positive mindset
Mélignon expects the transition to electric mobility to continue in 2025: "When I look at corporate customers, I see that 80% of all new orders are electric. This is quite different from the private market, where we barely reach 20%. The electrification of the Belgian fleet is therefore mainly driven by companies. I see that the government has recently made some announcements and initiatives to slightly adjust and refine the federal mobility budget. In the coming months, more and more people may thus give up their company cars and opt for this adjusted budget instead. Arval can also be of service there, with a positive mindset and a lot of know-how, in our role as a 'full mobility provider'."
Tipping point
According to Mélignon, the shift to electric mobility, which the market has been anticipating for so long, will also have consequences for companies. Mélignon: "We expect to see many more affordable models in 2025. Electric vehicles will no longer be just for the lucky few. This benefits the private market, but it also gives companies more opportunities. In addition, I expect the price of cars with combustion engines to rise. We often receive this feedback from manufacturers. As a result of the Corporate Average Fuel Economy (CAFE) standards, which regulate their CO2 emissions, they will soon have to pay huge fines if they fail to meet these standards. It is therefore in their interest to steer the market towards electric cars. They will also adjust their production capacity accordingly: 'made to order' instead of holding large stocks will become the industry standard from next year."
The road ahead
On a final note, Arval expects the market to open up to smaller and medium-sized enterprises and individual clients in the near future. Mélignon: "We believe that the change in the market will mean that many companies, which currently still favour purchasing company cars or financial leasing, will switch to operational leasing. They will outsource the risk related to, for example, residual value to us. And that is where we can make a difference as the market leader: we see this as a scenario for the near future, for which we are already preparing."